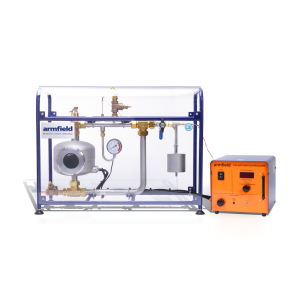
TH3 – SATURATION PRESSURE
The Armfield Saturation Pressure Apparatus has been designed to introduce students to how the temperature of water behaves at its boiling point with variation in the absolute pressure.
The TH3 offers all the features of a Marcet Boiler and adds the capability of determining the quality of wet steam, thus enhancing the understanding of the underlying thermodynamic principle.
DESCRIPTION
A bench top unit designed to introduce students to the characteristics of saturated water vapour.
The apparatus is equivalent to a Marcet Boiler, with an additional throttling calorimeter and a pipe loop, which enables saturated steam to be returned to the base of the boiler as condensate.
Pure water in the boiler is heated to its boiling point using a pair of cartridge heaters with variable power control. A sight glass on the front of the boiler enables the internal processes to be observed, namely boiling patterns at the surface of the water, and also permits the water level in the boiler to be monitored.
Saturated steam leaving the top of the boiler passes around the pipe loop before condensing and returning to the base of the boiler for reheating. The operating range of the boiler and loop is 0 – 7 bar. The top limb of the pipe loop incorporates a Platinum Resistance Thermometer (PRT), temperature sensor and an electronic pressure sensor to measure the properties of the saturated steam. A filling point on the top limb enables the loop to be filled with pure water and permits all air to be vented safely before sealing the loop for pressurised measurements.
A vapour offtake, with isolating valve, enables steam from within the loop to be passed through a throttling calorimeter, the purpose of which is to demonstrate how the dryness fraction of the saturated steam in the
loop can be determined.
The steam expands to atmospheric pressure as it is throttled and a second PRT temperature sensor measures the temperature of the steam following expansion.
The apparatus is designed for safe operation with a pressure relief valve set to operate if the pressure rises above the working pressure and a Bourdon gauge that remains operational when power is disconnected from the electrical console.
All power supplies, signal conditioning, circuitry etc. are contained in an electrical console with appropriate current protection devices and an RCD for operator protection. Readings from the sensors are displayed on a common digital meter with selector switch and all corresponding signals are routed to an I/O port for connection to a PC using an optional parallel interface/educational software package.